QC活動が工場でうまくいかない原因。管理職がとるべき対策とは?
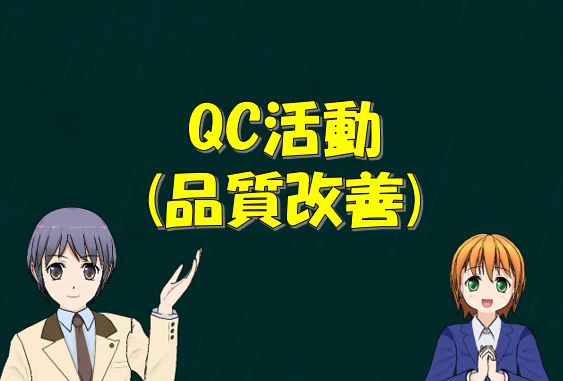
会社の品質管理を高めるためにQC活動(QCサークル)は多くの工場で行われています。
QC活動自体は7つ道具やQCストーリーなど優れた方法ではあるのに、実際にはうまく成果が上がらないことが多いと悩むことはないでしょうか。
僕は現在の会社の入社半年後にQC事務局を経験し、その後もリーダーを3回ほど務めました。
その経験から「これがQC活動がうまくいかない原因」と思ったことがありますので、この記事ではその原因と対策をお伝えします。
【QC活動について】
工場での品質管理は絶対必要なこと。しかし社員はQC活動を「なんとなく」で活動している
QC活動がうまくいかない原因
QC活動がうまくいかない原因としては以下の7つの項目を挙げられます。
- 工場では毎日改善をしている
- 目的が分からない
- メンバー構成
- QC7つ道具
- QCストーリー
- 上司が否定的
- 評価基準
これらについて一つずつ解説していきます。
業務の改善は工場では毎日やっている
工場で勤務する従業員にとって業務改善は当たり前の業務です。
『検査漏れ→チェックシートの作成』
『再製作→不具合報告書』
『目に鉄粉が入る→保護メガネの着用』
従業員にとって毎日が改善のため、QC活動といってもモチベーションがかなり低いです。
吉良
目的が明確でない
先ほどの続きともなるのですが、「なぜQC活動をするのか」「何をすればいいのか」というのが理解していないことがほとんどです。
僕の会社ではQC活動といっても品質に関係なくても良いと定義され、作業の効率化やムダ削減やコスト削減になるのであればいいとされています。
しかし、実際に僕がリーダーを務めたときにチームでテーマを決めると、
と方向転換されました。
実際は上司の言うことも正論ですが、それは最初に言うべきものです。
工場では毎日改善をしているため、QC活動では普段の業務では改善できないことをすることが望ましいです。
例えば「工場のレイアウト変更」「新規導入設備の活用法」など。対策をするのに時間がかかるものをテーマにするべきです。
メンバー構成が適当
過去に実際にあったのが「工場のレイアウト変更」というテーマを組立が取り組んでいたのに、全く進まず中途半端に終わったということ。
実際には複数の部署に影響するのに、メンバーは組立の中の4人ほど。しかも上司は実質何もしていません。
本来であればレイアウトに関わる部署のメンバーを一人ずつは代表で必要ですし、工場長などへ進言することができるベテランも必要です。
QC活動って新人や若手がメンバーになることが本当に多いですよね・・・
春川
取り組むテーマが「そのメンバーで不可能」と判断されれば、他部署から補充なども検討が必要です。
吉良
QC7つ道具を名前しか知らない
QC7つ道具と言っても現在は8つ存在します。
名称 | 説明 |
パレード図 | 全体の中大きな影響を及ぼすものを把握 |
統制要因図 | 魚の背骨のような形を書き、問題の要因を探す |
グラフ | データの比較で視覚的に表現 |
チェックシート | データの種類や項目ごとにチェック |
ヒストグラム | 工程のばらつきを調べる |
散布図 | 2つのデータの関係性を調べる |
層別 | グループ別に分けて問題点を把握 |
管理図 | 現在の工程が正常化を判断 |
僕の会社では過去のQCの発表データから特性要因図はよく見ていましたが、みんな真似をするだけで何となくやっていました。
QCストーリーを知らない
QC活動においてQCストーリーは有名な手法です。
しかし、実際にQC活動のリーダーをしていた人たちは名前すら知らない人のほうが多いというのが現状でした。
上司が否定的
僕が入社2年目、初めてQCリーダーを任命されたときに工場長から言われた言葉がこれです。
当時必死に資料作りをしていた僕が言われた言葉です。
モチベーションの低下が生まれたのは言うまでもないでしょう。
ただし、その後も次長などからも似たような言葉を言われ、リーダーと管理職との間で温度差を感じました。
(取締役はQCを推奨)
評価基準が適当
QC活動をすれば必ず最後に発表があるでしょう。
僕の会社の場合はパワーポイントでの発表だったため、独学で自力で作りました。
そして感じたことは
ということ。
初めて僕が資料作りを担当したチームは、工場での業務の作業時間短縮(20分から10分へ)という成果を出してはいました。
しかし、パワーポイントの作成が全くど素人であったため、発表は残念ながらドベでした。
そして、優秀賞に選ばれたがチームは
「今回の費用5万円かかり、成果としては残念ながら以前よりもだめになりました。」
というような内容です。
しかし、資料作りがかなりプロっていて、QC7つ道具を使い、デザインやアニメーションもきれいです。
さらにその2年後にも評価基準が適当と分かるできごとがありました。
僕が過去の失敗から資料作りだけはかなり力を入れて、ほぼ一人だけで作ってしまったQC活動。
実績はないのに、部内で1位を獲得です。
こんな評価基準では誰も喜ぶ人はいません。
管理職の対策でQC活動は良くなる
ここからは具体的な対策をお伝えします。
結論を言うと先ほどの原因を解消する内容をすればいいです。
目的・方向性は最初に話す
まずはQC活動として何をゴールとしたいのかを明確にしましょう。
「最初が肝心」という言葉をよく耳にすると思いますが、最初にある程度指示をしておくことでテーマが全く変わります。
権限のある人。もしくは人脈のある人をメンバーに入れる
QC活動はよく新人や若手に押し付けます。
新しい発想が浮かぶというのはいいのですが、少し大きなことをしようとするとすぐに限界が起きます。
また、他部署との連携を取れるか取れないかがかなり重要となりますので、会社の中で人脈のある人が一人は必要です。
見本や手法を社員に見せる
QC7つ道具やQCストーリーをどのように使うのか。
会社の中で優れたチームに指導役を任せましょう。
また、社内で詳しい人がいないのであれば他の会社から講習をしてもらうのも一つの方法です。
QCメンバーにできないことは上司がフォロー
工場のレイアウトなど、取り組んでいる内容が大きくなれば必ず管理職の出番がきます。
QCリーダーが工場長へ相談に行くのは当然ですが、若手がリーダーを務めた場合は大体否定から始まります。
会社の中でも上位の管理職と関係する場合は直属の上司のフォローが必要不可欠です。
評価基準を正確にする
会社の中で何を評価基準にしているのか。
- 実績の評価を優先
- QCの手法を取り組んでいるのか
- みんなで取り組んでいるのか
- 品質改善になるのか
- 嘘の報告はないか
評価基準はできれば明確にしましょう。
また、過去の経験によると「嘘をつくチーム」というのは必ずいて、しかも上位に入ります。
その発表が嘘をついていないのか。実績を大きく報告していないかなど審査できる人も必要です。
まとめ
この記事ではQC活動がうまくいかない原因についてお話しました。
QC活動【うまくいかないときは管理職も対策を】
- 目的・方向性は最初に話す
- 権限のある人。もしくは人脈のある人をメンバーに入れる
- 見本や手法を見せる
- 上司もフォローする
- 評価基準を正確にする
仕事術はないよりもあったほうが当然良いです。
以下の記事も参考にしましょう。